背景
Futureグループでは、「2Way戦略」と呼ばれるスローガンの元、今までのB2BだけでなくB2Cなど別の領域へ自らがサービスを提供し、ビジネスを広げていく事を目指した活動が盛んに行われています。
まだまだ、ローンチされたサービスは少ないのですが、その中の1つであるBluetoothのビーコンを使ったIoT系就活サービスの「縁採Quest」(エントリクエスト公式サイト, Google Play, App Store)で、3Dプリンタを使ったモノづくりをしたので、その時の3Dプリンタに関する話をしたいと思います。
「縁採Quest(エントリークエスト)」って?!
縁採Questは、地方にいながらロールモデルとなる社会人を見つけて深く繋がっていく、ということを目指したサービスになります。
弊社は採用に非常に力を入れている会社なのですが「今の就活はおかしいのではないか?」という問題意識を複数の社員が持ったことがサービス誕生の背景です。
この「Webページでクリックするだけの就活ってどうなのよ?!」という所に一石を投じるために、あえてローカルな場所に縛った就活を展開する事によって、今まで知らなかった働き方や、人との出会いに偶然を生み出して学生さんと会社を結ぼうとしています。
この中で「ローカルな場所に縛る」ために、Bluetoothのビーコンを飲食店、インキュベーション施設などに配置して、そこでしか得られない情報や結びを提供していこうとしています。
このBluetoothのビーコンの事を「縁採タグ」(エントリータグ)と呼んでいます。この縁採タグのケース製造に3Dプリンタを活用しました。
3Dプリンタを使った縁採タグの作り方
今回は3Dプリンタに焦点を当てるので、中の電気回路の部分は省きますがそこにも様々なドラマがありました。
- 国内の認証を通っているBluetoothの部品を集めるところ
- 基板を中国に発注したけれども、パターンが小さすぎて対応業者が少ないという話
- ホットプレートリフローやるのは小さい部品は厳しいという課題を乗り切った話
- クリーム半田はどこで調達しようか悩んだこと
- etc.
それぞれについて詳しくお話したいですが、それはまた別の機会に。
ということで、縁採タグの完成品はこれです。
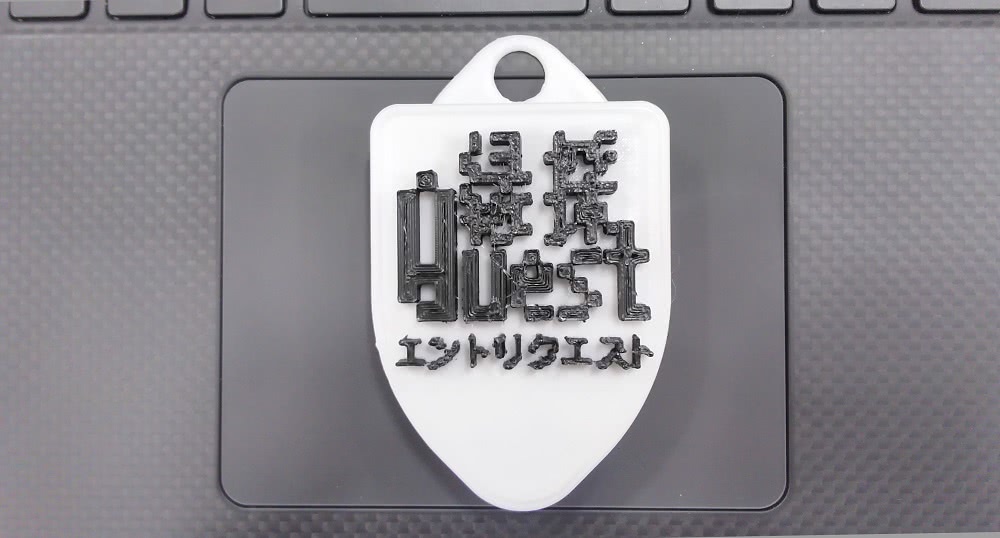
小さめのマウスぐらいのサイズで、白いところはポリカーボネートという丈夫な素材で作りました。黒いところは、PLAというトウモロコシなどから作られる環境に優しい材料です。2つの材料を同時に出力できる3Dプリンタを使って作っています。
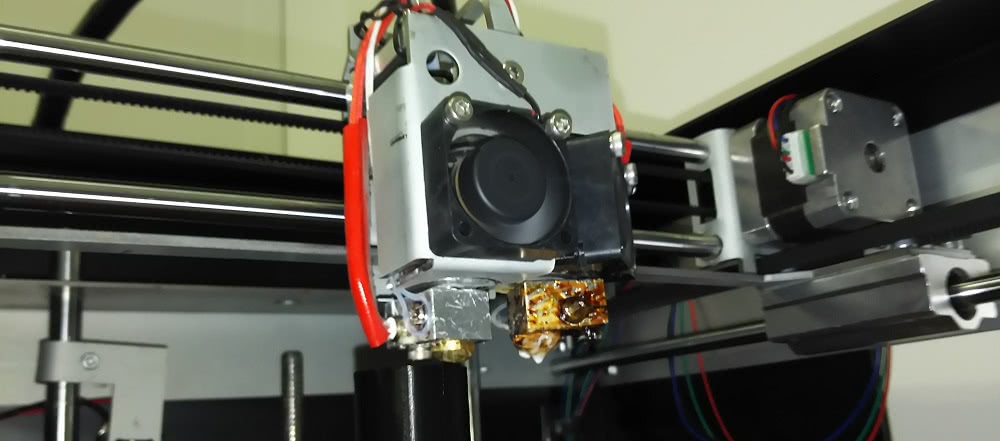
けなげな3Dプリンタは0,4mmのノズルから材料を熱で溶かしながら0.2mmの高さで積み重ねていきました。
最終的な高さは20mm程度あるので、100層分積み重ねてできあがっています。
だいたい1タグ4時間ぐらいかけて印刷していました。全部でこの写真のモデルは30個ぐらい作成しています(今はまだ改良版の制作に取りかかっているので、プリンタは大忙しです)。
3Dプリントの難しかったところ
いろいろあったのですが、特に印象に残っている、こんなことに苦労したというのを4つ紹介します。
(1) ポリカーボネート
本体のケースなので、ある程度耐久性を考慮してポリカーボネートという材料を今回選択しました。使ったのはポリメーカーのPC-MAXというフィラメントです。たまたま別のモノづくりで買っていた材料があったのですが、Amazonで売り切れているときは他でも売り切れていることが多くて、海外から直接購入することもありました。今は国際物流がしっかりしているので、DHLとかフェデックスとかへ、ちゃんと送料支払えば2日ぐらいで手に入るので便利な世の中になってます。ポリメーカーは中国から配送されるので、距離的にも近いので国際配送でも結構いい感じです。
材料は手に入ったとして、次に問題になるのは3Dプリンタです。
ポリカーボネートは、通常の3Dプリンタよりも高温にできるいわゆる「エンプラ」対応の3Dプリンタでないと印刷できません。
エンプラ?!
エンジニアリングプラスチックの略称です。100度以上の温度に耐えるとか、丈夫とかいろいろ優れているよっていうプラスチックを総称する言葉です。3Dプリンタでエンプラ対応というのは300度の温度で印刷が行える機種が必要です。今回は、Genkei社のLeptonを利用しました。高温対応バレルを装備させると、この3Dプリンタはエンプラ対応になります。おまけに、2射出機構も付けているので、文字と本体で色を変えて印刷することにもチャレンジしています。
(2) 文字を綺麗に出すために
文字の部分を綺麗に出すために、2点ほど工夫が入ってます。
白の台座を用意
今回のパーツでは、文字の点が飛び飛びで存在するので、その点と点の間を移動するときに黒のノズルが白い本体をこすってしまい、黒い線が出てくることが分かりました。
黒い文字の印刷をする最中の移動時に1回1回Zホップさせてノズルを印刷済みの本体から引き離して印刷してみたのですが、印刷時間が増えるとともに文字の印刷品質が落ちてしまいました(ひどい糸引きが発生する。文字の壁がでこぼこになるなど)。
これは、ノズルを真横に移動させて拭き取る動作が行われないために、うまく材料が切れなくて発生していたようで、長いこと問題が解決できませんでした。
しかし、Zホップさせないと、白いケースの上面に黒い線が残ってしまい、それはそれで問題が残ってしまいます。
この問題は、白の材料で台座の出力までさせることでどうにか解決させました。
この画像にあるように、上の明るい黄色の部分を黒い材料で出すのですが、その下に、白い材料で台座を印刷して広い平面と高さを変えるようにしました。これにより、黒のノズルが移動するときに白の平面をこすることがなくなったので、綺麗に印刷できるようになりました。
あちらを立てればこちらが立たずで、最後まで苦労したところです。
(3) 黒の材料の選別
文字を出力する、黒い材料ですが5種類ぐらい購入して印刷を試してみました。やはりメーカーにより材料の特性が異なるので、一番良い材料に巡り会うまで大変でした。
柔らかくて糸引きが多い材料とか、表面は綺麗なんだけど切れが悪いとか、小さい文字を出すときは材料の特性が最終的な品質に与える影響が大きくなるので、選定は慎重さが必要です。
(4) ヒートベッドが離れていく
さあ、いざうまく1つ出せるようになったのですが、その後量産をするためにまとめて出そうとしたら、印刷途中でモータが脱調したりなにがしかの不具合が出て、途中でうまく印刷できなくなってしまいました。
成功するときもあって、何が起きて失敗しているのか問題を切り分けていったら、印刷時間がある閾値を超えると失敗する事が見えてきました。
なので、まとめて3個ケースを出しているときとかは簡単に失敗してしまい、1個ずつ出すという効率の悪い方法でしのいでいました。
その後、1個だしでも、連続して印刷をしていると失敗することが分かり、これはヒートベッドの温度が問題ではないかと当たりがついてきました。
というのも、今回ポリカーボネートを出すために、ヒートベッドを120度まで暖めていました。これは、BuildTakというシートを使わないでポリカーボネートを印刷するために編み出したコツで、120度+ブリムでBuildTak無しでもどうにか印刷できています。一部浮き上がっているところもあるのですが、今回は許容範囲内なのでこれでガンガン印刷しています。
そのため、120度という少し高温にヒートベッドを加熱していてその加熱により金属膨張が下方向に働いてヒートベッドとノズルの隙間が空いてしまい、うまく印刷できない現象が発生していました。
これはFusion360という3D-CADソフトで熱解析も行って裏をとっています。
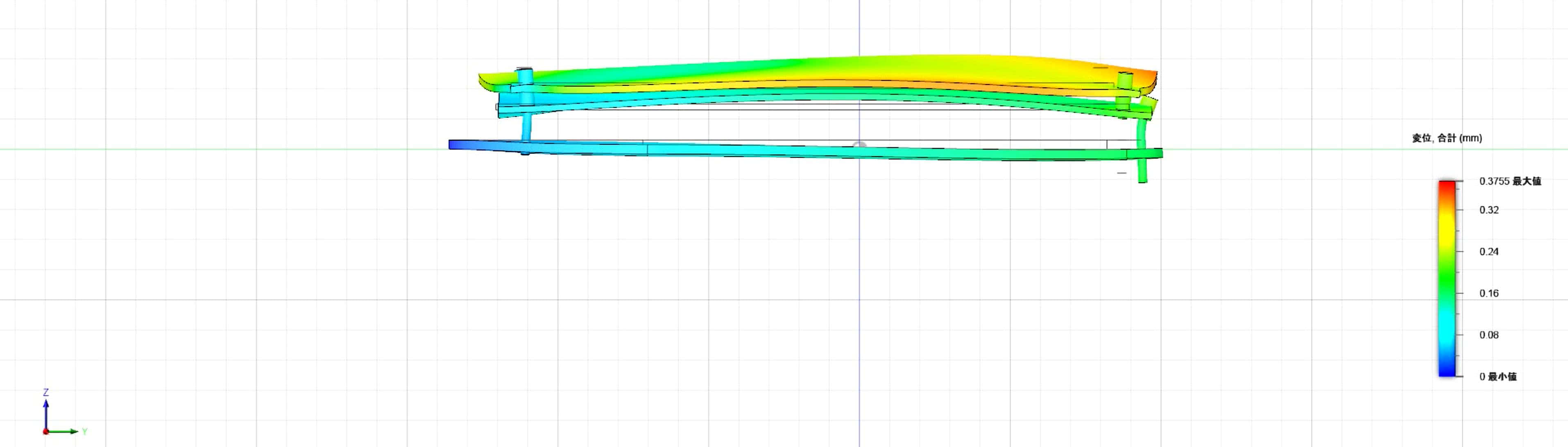
そこで、ヒートベッドの裏側にグラスウールの断熱材を貼り付けてみました。
貼り付けると嘘のように連続印刷が問題なく行えるようになりました。熱膨張、皆さんも甘く見ないように気をつけてください。
結局、3Dプリンタを使って良かったと思う
なんだかんだ、問題もたくさん発生しましたがポリカーボネートを出すことに関してかなり自信がついてきました。材料自体は特性が良いので、ノズルで詰まると言うことも全く発生していませんし、印刷後の加工に関してもPLAよりも加工しやすいと感じています。
コスト&修正サイクル
縁採タグは見た目こそ小さいですが、これがあるのと無いのではこの就活サービスを宣伝するときのインパクトが違うと言うことで、かなり良い営業ツールになっています。
はじめから金型作って、2つの樹脂を流し込んでとかやっていると、それだけで軽く100万円ぐらいかかります。
今回使った3Dプリンタは20万ほどで購入できるので、5分の1です。
さらに金型だと、デザイン変更をしたり内部の形を変えるたびに、この費用がかかってきます。また金型を作って製品ができあがるまでのリードタイムも2週間ぐらいかかったりするので、かなりヘビーです。
設計を変更したら、すぐに印刷、お昼から帰ってくるとできあがっているなんてことも、普通に出来るので高速に改良を加えられ本当にトライアンドエラーで進めていくスタートアップ向きです。
そして、モノづくりは簡単になった
金型ありきの製品開発でトライアンドエラーなんて時間もコストもかかったので今までは無理だったのがよくわかります。だからモノづくりはウォーターフォール型の開発が主流なんですよね。
しかし、そこに今回は3Dプリンタを使ったことで、モノづくりをアジャイル開発的に手軽・高速に行えるようになりました。
最終製品に関するこだわりとか、表面の綺麗さとか考えていくと、今までのモノづくりの方が良いという所も多いと思いますが、熱積層タイプの安価な3Dプリンタで最終製品を作るという事もアリだなと今回のサービス開発に関わってモノづくりをする中で感じました。
皆さんも、簡単になったモノづくりに是非チャレンジしてみてはいかがでしょうか。
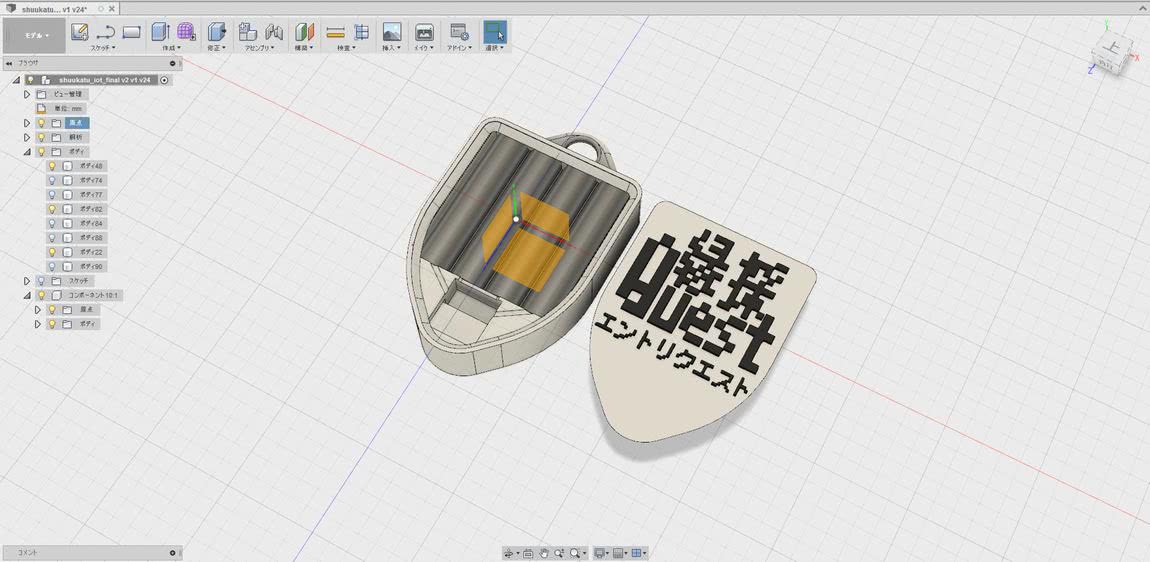